
process optimization
The process is running but ...
- Production costs too high
- Too high error rate
- Cycle time / cycle time too long
- Too high stocks
We find and use the potential for improvement ...
Depending on the project size, the methodology is chosen:
- audit
- We work pragmatically and adapt the methods and objectives to your product portfolio and the needs of your customers.
- The optimized process will be characterized by high efficiency and, above all, as a self-optimizing system (continuous improvement process).
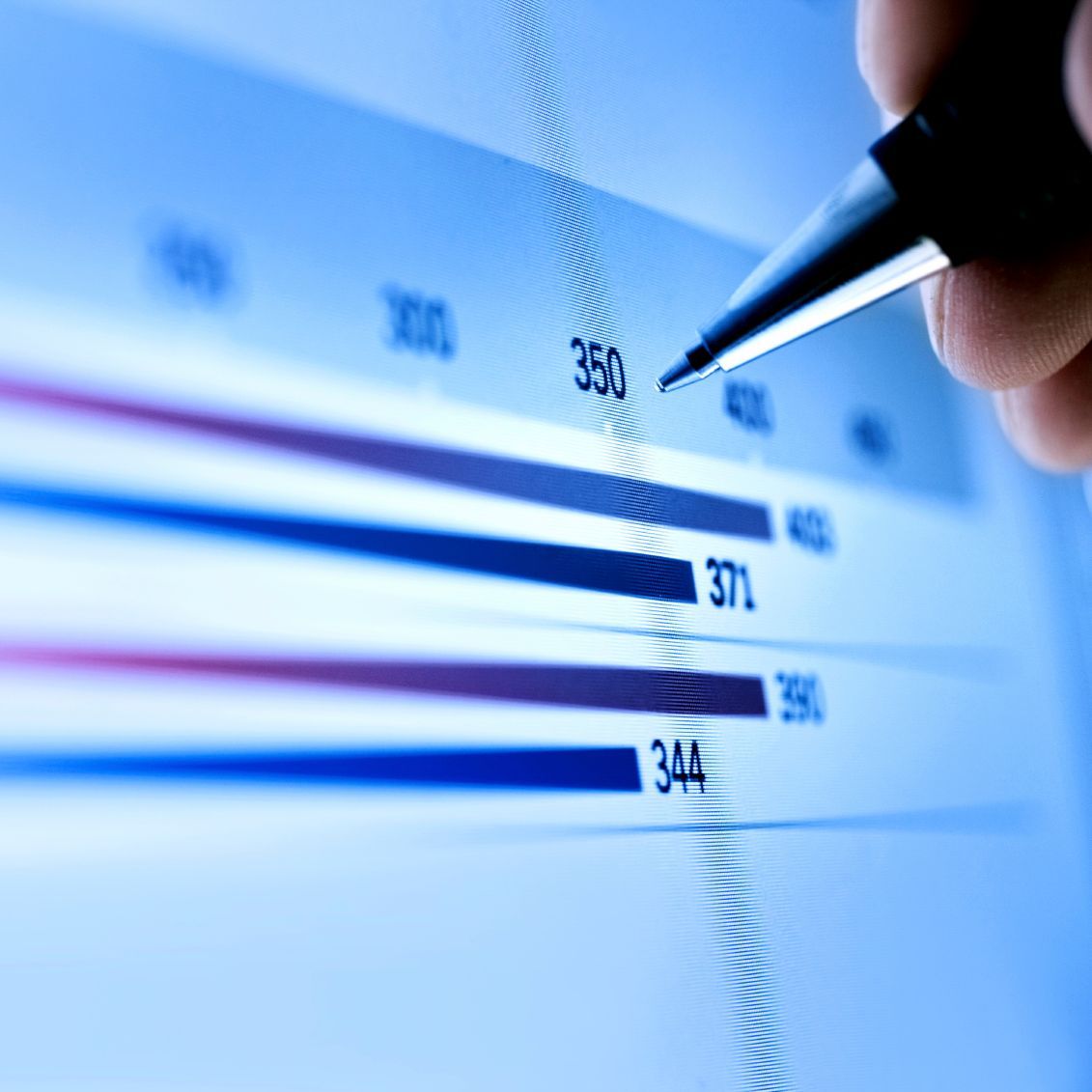
Continuous improvement process
Mistakes are only bad if you do these two times, so we promote your error culture under the motto:
"The crap we build every day can bear fruit,
when we use it as a fertilizer for our becoming better "
Ernst Ferstl
A positive error culture is a success factor
- Are you on the road to business excellence and looking for a comprehensive improvement?
- Then it will require more than process optimization.
- All kinds of waste (error rates, waiting times, stocks, distance, etc.) must be continually reduced further.
- What is needed is an automatism that makes permanent optimization a method.
- This is the basic element of any quality management system, the KVP.
- We develop with you a system that makes the permanent optimization a self-running.
- Not a standard system, but a method that is tailored to your needs
- By means of a Pareto analysis, the improvement potential of your individual process steps is determined so that the KVP introduction starts at a few, but very important key points.
- The core point is a control loop (measure-analyze-improve). For example, shown as PDCA cycle or deming circuit.
- We train your employees
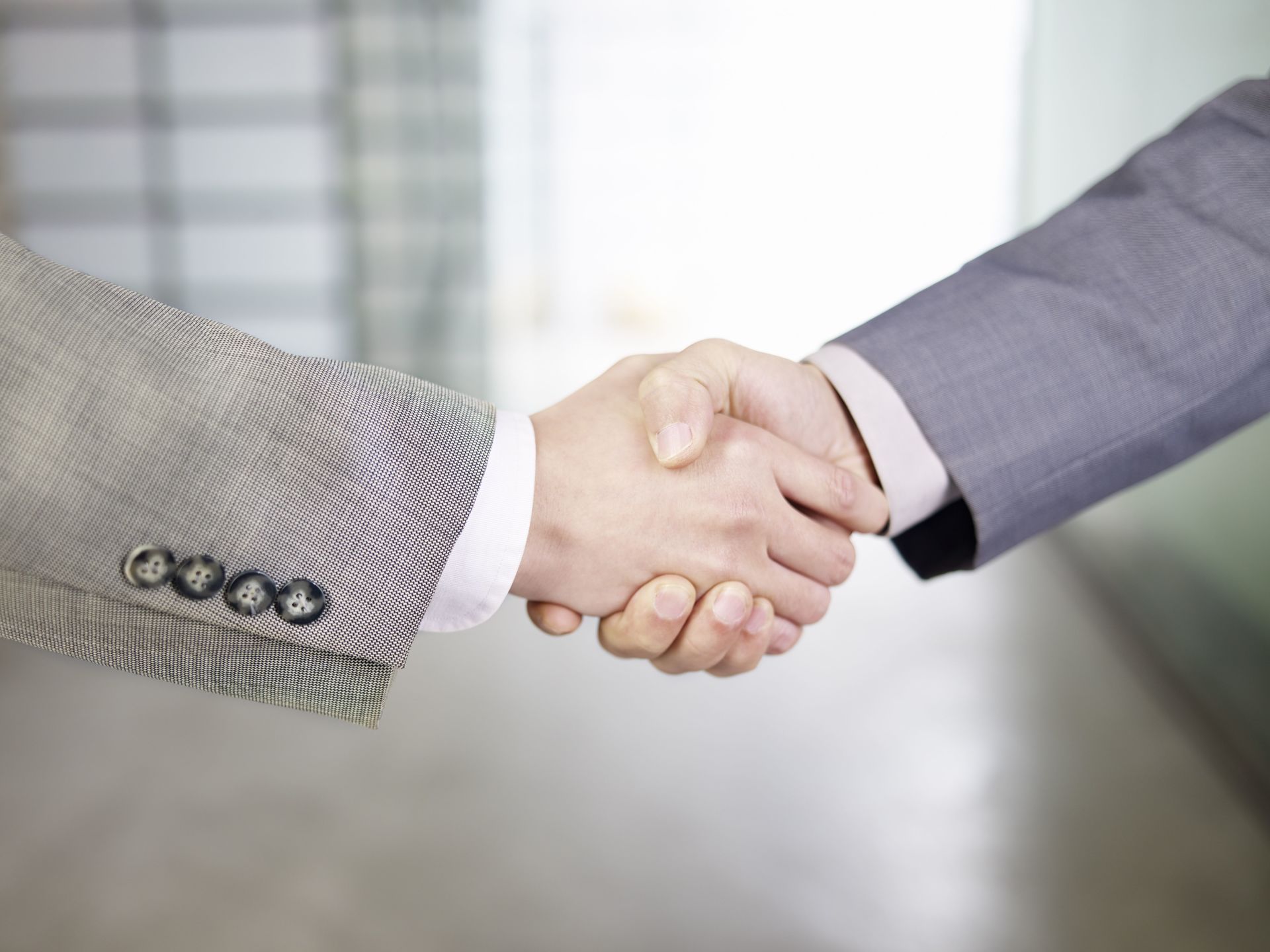
supplier management
- Your supplier should be checked routinely ...
- Your supplier does not do what he is supposed to do
- Error rate, delivery ...
- You want to change the supplier and have to have an exact picture of the new one ...
- Your supplier will deliver a new product. The serial start must be absolutely secure ...
- We audit the supplier on site, elaborate necessary measures and monitor their implementation.
- Similar to process optimization.
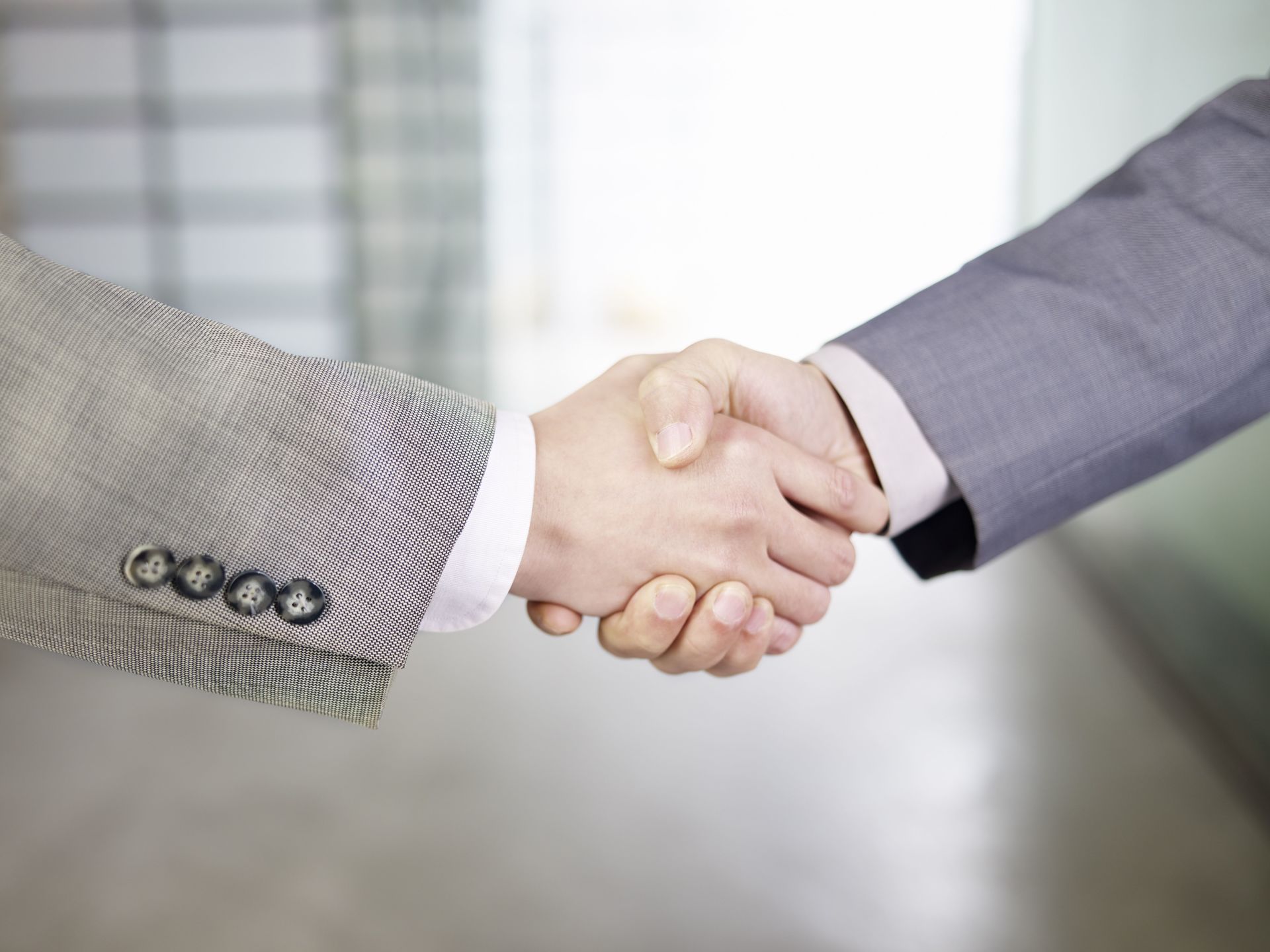
risk management
- A very important decision (new project, large invest ...) is on. They want to hedge themselves and to present the risks in figures
- Or crassier: The decision has already been made, now the risk has to be assessed
- They want to prove the safety of a construction
- We examine the process methodically. SWOT analysis, FMEA, value analysis and similar methods are applied
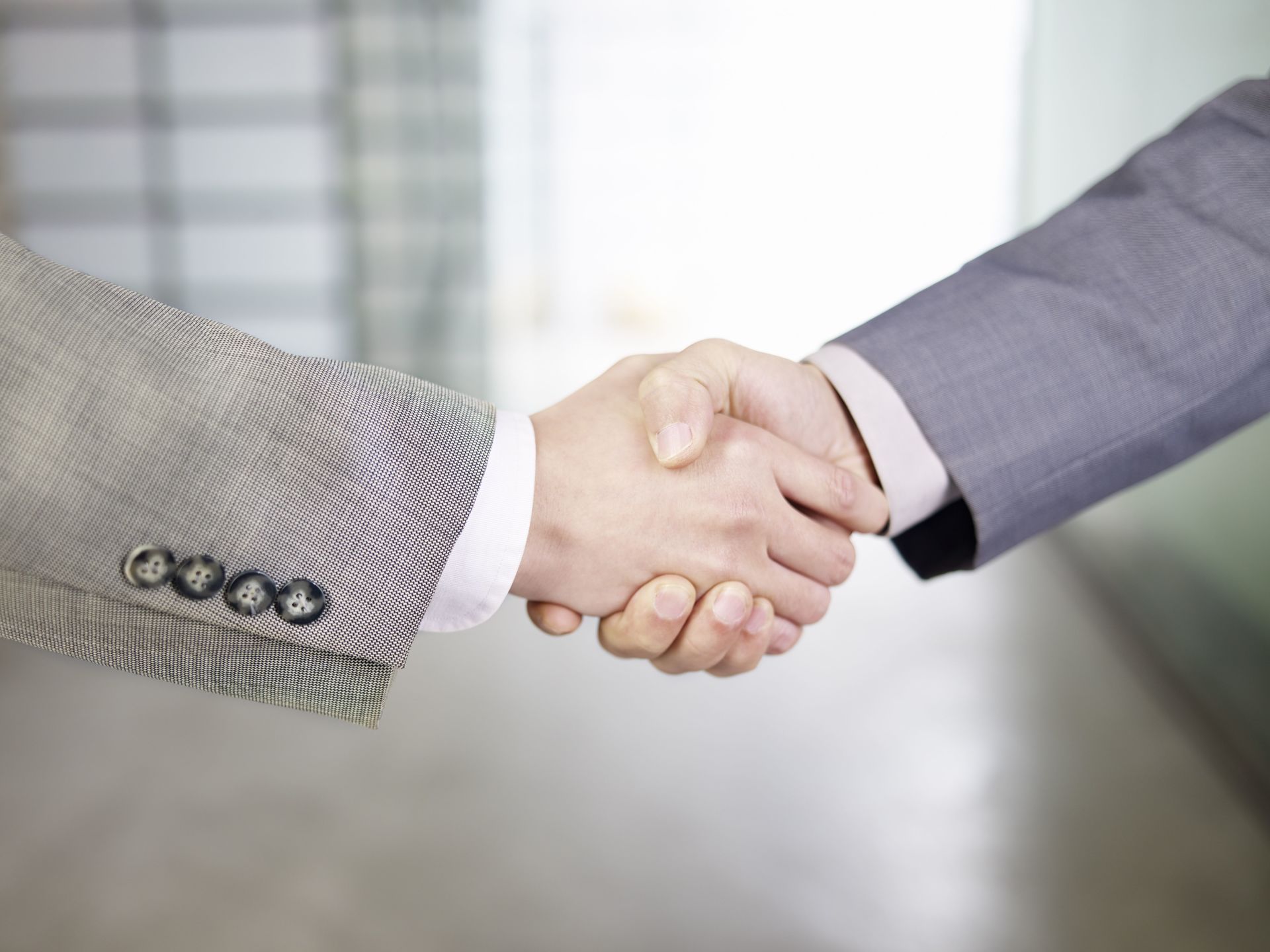
Incident management and fault analysis
- Again and again "mysterious" mistakes occur in products or processes. The costs are rising, customers are upset. The cause is unclear and you have no capacity for complex examinations.
- It is true that mistakes are not phenomena, but physically explainable processes.
- A systematic approach, eg Ishikawa analysis (herringbone diagram, 5M method) or by an error tree analysis (FTA), will also unmask the most stubborn errors.
- On request, we can carry out the required removal measures and appropriate fault-prevention measures. (8D report, FMEA ...)